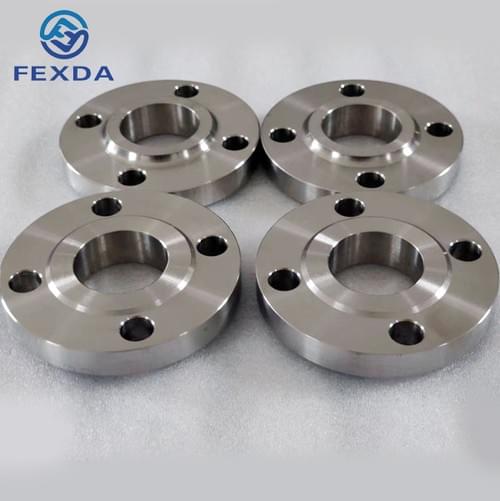
TITANIUM FLANGE
--------------------------------------------------------------------
Grade: Gr.1, Gr.2, Gr.3, Gr.4, Gr.5 Gr.7, Gr.9, Gr.12
Type: Plate, threaded, slip-on, socket welding, lap joint, blind, welding neck …etc.
Specification: DN15-DN2000
Pressure: PN0.25-32Mpa (Class150-Class2500)
Flange sealing face: FF,RF,TG,RJ… etc
Technique: Forged, CNC machined
Price: Acc. to each unit, qty’ and other special request of clients.
Application fields: Water conservancy, electricity, pressure vessels, petroleum, chemical, shipbuilding, metallurgy, machinery, stamping elbow and other industries.
What is Flanges?
Flanges are the second most reliable method which is used for joining after welding. The most reliable method is abviously the valves system. The usage of flanges adds a high level of flexibility in order to maintain a proper systems by allowing the easier disassembly an improved access to the components of a system.
6 Common Types of Flanges
Flanges are of various types which can be selected according to the site requirement. Scroll down to have a look at the most common flange types which are usually available.
(1),Threaded Flanges
These are the flanges which are also referred to as a screwed flange and is found having a thread inside the flange bore that gets fit with the matching male thread on the fitting. The threaded connection here refers to as avoiding the welding in various cases. It is mostly connected by matching the threading to the pipes which is to be installed.
(2),Socket Weld Flanges
This type of flanges are usually used for smaller pipe wherein the diameters in low-temperature and low-pressure areas feature a connection in which the pipe is placed inside the flange in order to secure the connection with a single or multi-pass fillet weld. This is responsible for making the style simple in installing as compared to other welded flange types by avoiding the limitations that are associated with the threaded ends.
(3),Lap Joint Flanges
A Lap joint flange is the one which requires a butt welding of the stub end to that of a fitting in order to use it with a backing flange and to create the flanged connection. This design is responsible for making this style popular for use in various systems which are found having a limited physical space or systems that requires a frequent dismantling or high maintenance.
(4), Slip On Flanges
Slip-on flanges are found to be very common and also available in a wide range of sizes in order to accommodate the systems with high rate of flow and throughput. It is quite easy to install it by simply matching the flange with the outer diameter of the pipe in order to connect it. Installing these flanges is a bit technical as there is a need of fillet weld on the both side in order to secure the flange to the pipe.
(5),Blind Flanges
These type of flanges are highly used for terminating the piping system. The blind flanges are found to be shaped like a boltable blank disc. Once these are installed properly and combined with the correct gaskets, it can achieve an outstanding seal which is easy to remove whenever required.
(6),Weld Neck Flanges
Weld neck flanges are quite similar to lap joint flanges but require a butt welding for installation. Whereas the integrity in the performance of this system along with the multiple repeat bends and the ability to use them in high-pressure and high-temperature systems makes them a leading choice for process piping.
Flange Face Types
Face types are also quite important characteristic which is found having a major impact at the final performance as well as service life of the flanges. Therefore below are mentioned some of the most important types of flange facing.Flange Face Types.
(1),Flat Face (FF)
It can be clearly predicted from the name that the flat face flanges are found having a flat and even surface which is combined with a full face gasket which contacts almost all the flange surfaces.
(2),Ring Joint Face (RJ)
These are the face flanges which are used in high-pressure and high-temperature processes. This face type is the one which has a groove in which a metal gasket sits in order to maintain the seal.
(3),Raised Face (RF)
These are the types of flanges which have a small raised section near the bore with an inside bore circle gasket.
(4), Male & Female (MF)
These types of flanges are quite similar to the tongue and groove flanges which uses a matching pair of grooves and raised sections in order to secure the gasket. These retain the gasket on the female face which provides more accurate placement as well as increased options of the gasket material.
(5), Tongue and Groove (TG)
These are the flanges which inculcate a matching grooves and raised sections. This aids in installing as the design helps the flanges in order to align and provide a reservoir for the gasket adhesive.